Adding details to parts in Directline is an important step to ensuring your inventory is comprehensive. With the use of the quantity, reorder, and location fields – parts can always be on hand and accessible for all staff when required.
Navigation
To access the Inventory Detail Entry screen simply navigate to it via:
- Module
- Inventory
- Inventory
- Inventory Detail Entry
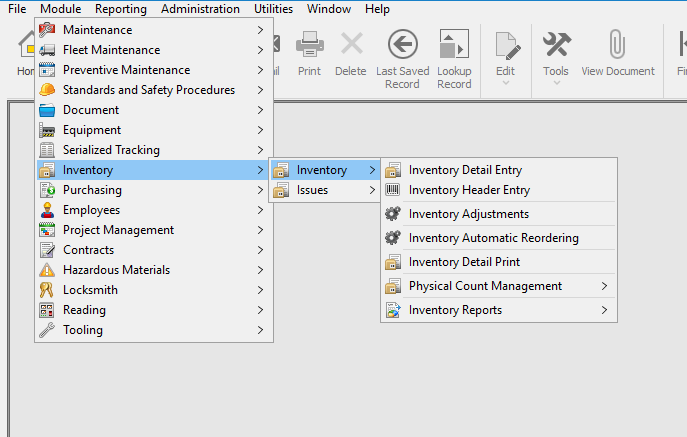
Inventory Detail Entry Process Flow
- Mandatory Fields >
- Recommended Fields >
- Optional Fields >
- Details Tab >
- Save
These Fields are noted by an asterisk on the label as well as the field being highlighted in green.
On the Inventory Detail Entry Screen there are 2 mandatory field(s):
Part# – This is the unique identifier for the Inventory record. This ID can be made up of Letters, Numbers, and dashes or underscores. No spaces or other special characters are allowed. Usually a Part# has already been created using the Inventory Header Entry screen prior to adding details to a part. Click Here for more information on creating a new part using the Inventory Header Entry screen.
Warehouse – The warehouse field designates which location this piece of inventory resides in. This can be either a physical warehouse or simply any building in which the part is located.
Aside from Mandatory fields, there are others that provide valuable information to the end user. Here are a few of these:
Maximum & Minimum Quantity– These fields control the maximum and minimum quantities of the piece of inventory in the current warehouse.
On-Hand Quantity (OHQ) – The OHQ can either be updated manually or automatically and it tells the system if a piece of inventory needs to be reordered if the current OHQ is below the Minimum Quantity.
Supplier – Supplier information is an important part of the Inventory Detail Entry. This group of fields identifies where the part is coming from, supplier part#, the unit of measurement (UOM) as well as the lead time.
These are all other fields on the screen which will add more detail to a part but are not required. Some optional fields include – Aisle, Shelf, Bin, Reorder Quantity, Account# etc. It is recommended to make use of as many optional fields as possible to make your inventory records more detailed.
The Details tab of the Inventory Detail Entry screen provides some additional information, the three field blocks in this tab include:
Related Equipment– This field block can be used to display which equipment the current part can be used in, for example toner cartridge may be used in several different printers in the office.
Physical Count Particulars– Most of the fields in this block update automatically from physical counts performed on inventory.
Substitute Parts– A fairly self explanatory section which simply indicates if another piece of inventory can be used instead of the current piece.
Once all Mandatory and chosen Optional fields have been entered simply use the button on the Directline toolbar to create this new piece of inventory.